Post by PitYak Studios on Sept 27, 2006 11:44:37 GMT 12
The keyless chucks I sell are Dremel brand, and fit some models without any problems at all. Other rotary tools will often be able to utilise these chucks, but it may require a bit of thought and improvisation on the part of the tinkerer buying the chuck. Here's one way of getting the chucks to work with non-standard tools.
I'm trying to get the chuck to fit this battery operated Dremel. (Nice cheap little tools, I've got two, one of which I've jury rigged for mains power).
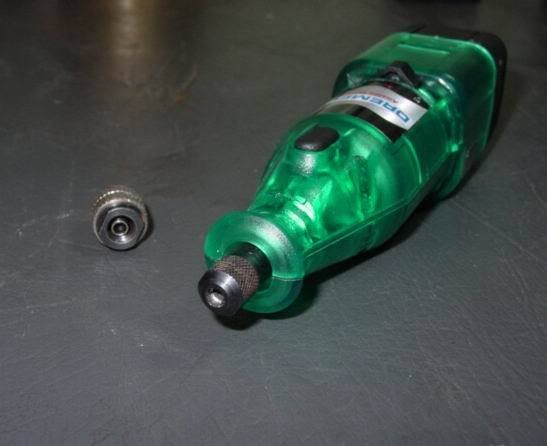
This pic also shows the bottom of the chuck; note the small tubey thing in the centre, that will be important later.
There are typically two reasons why your chuck won't work with your tool. (OK, actually there's three, I'll deal with one right now...)
If your tool has a different size thread to the chuck, you are going to find it incredibly difficult to get the two to fit together, so for the sake of this tute, just forget it. Below I've taken the collet off the tool, and checking the thread against the chuck, it looks like we are in business so I can continue.
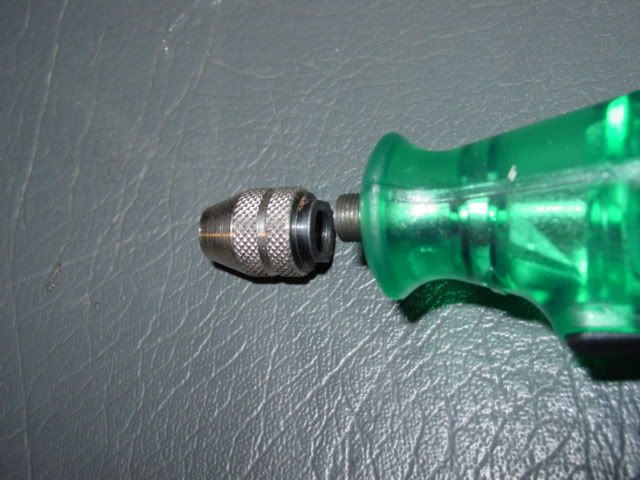
This next pic shows the chuck fitted to the tool, but as you may be able to see, The finger guard is preventing the chuck from being screwed down the thread far enough.
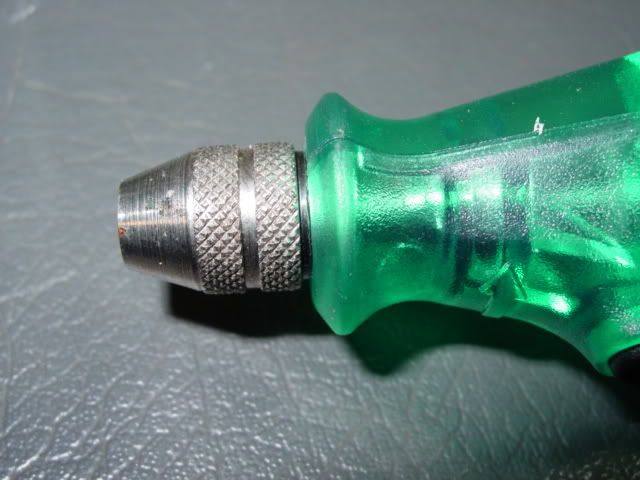
Time for our first bit of surgery. The finger guard, as the name suggests, protects your fingers, but doesn't have any other effect on the operation of the tool. Most rotary tools have removable finger guards, but this little budget fella doesn't, so out comes Mr Hacksaw. I removed the case , then sawed the guard section of both halves before re-assembling.
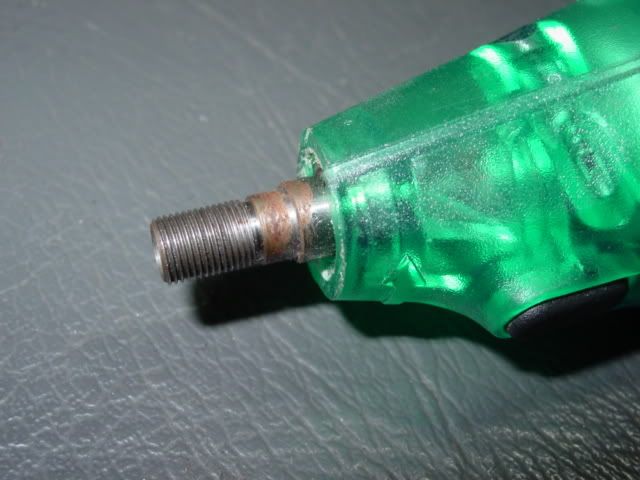
(Now at this point I must stress that I'm not suggesting you take a saw to your expensive power tools, and removing guards is obviously inherently dangerous and good for warranty-voiding. This tute is just for novely information purposes
This is what worked for me, and in any case the finished drill will be bench mounted to take buff wheels and the like, so the lack of a finger guard is not important in this case)
Tadaa! The chuck now screws all the way down the thread! First success!
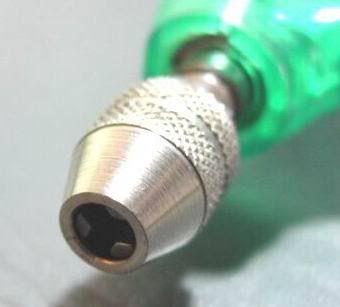
Ah, right. As the more observant of you may have noticed, even though the chuck is wound all the way down the thread, the jaws have not closed. Bit of a problem, as winding the chuck down the thread is supposedly how you close the jaws.
Look at the first pic again. That little circley thing in the centre of the chuck is the base of the jaw mechanism. As you turn the chuck down the thread, this should come into contact with the inside of the threaded bolt, and close the jaws. Must be that something is missing from our tool, and hence the chuck is not closing as it should.
What we need to do is find something that will fit down the centre of the bolt, and come into contact with jaws as the chuck is tightened. I've gone for a bit of brass rod, it was the exact diameter I needed, and with a bit of trial and error I was able to get the length right. I also rounded off the edges on the buffer to prevent any burrs from fouling the mechanism. You could probably use plastic rod, any sort of metal rod or tube, a section cut from a bolt. If you have a spare collet, like the one shown in the pic, you could use that; just hacksaw off the jaws.
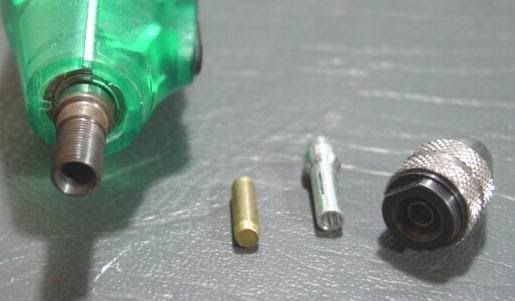
Slide the rod into the threaded bolt...
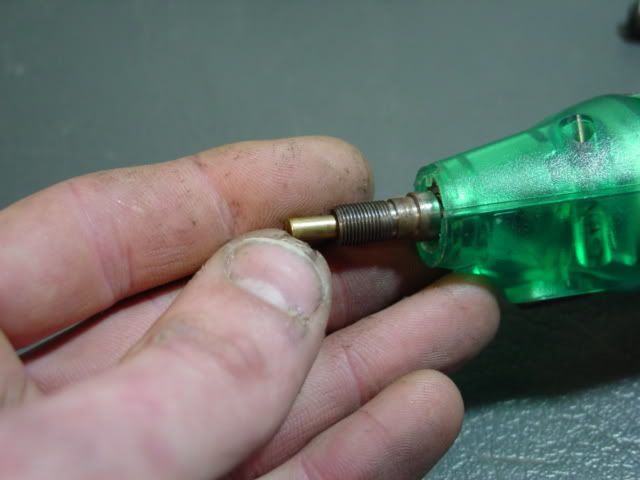
... wind on your chuck...
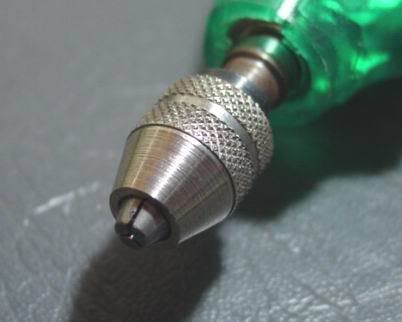
...et voila
I'm trying to get the chuck to fit this battery operated Dremel. (Nice cheap little tools, I've got two, one of which I've jury rigged for mains power).
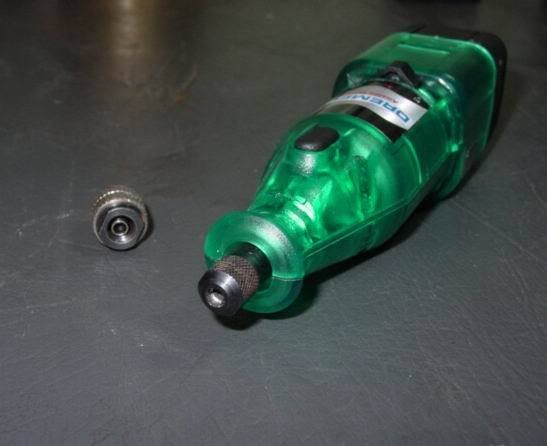
This pic also shows the bottom of the chuck; note the small tubey thing in the centre, that will be important later.
There are typically two reasons why your chuck won't work with your tool. (OK, actually there's three, I'll deal with one right now...)
If your tool has a different size thread to the chuck, you are going to find it incredibly difficult to get the two to fit together, so for the sake of this tute, just forget it. Below I've taken the collet off the tool, and checking the thread against the chuck, it looks like we are in business so I can continue.
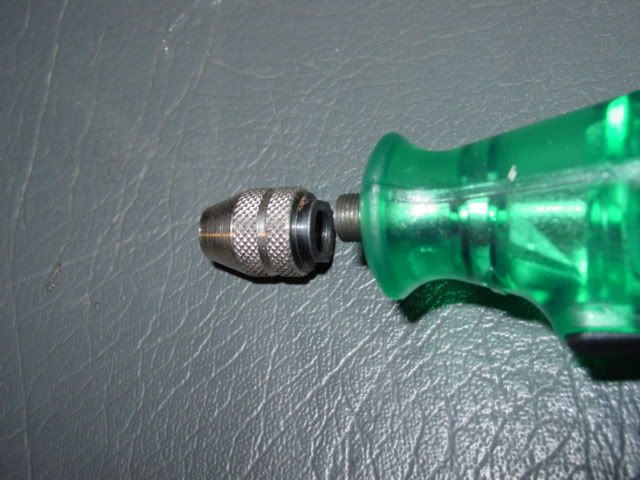
This next pic shows the chuck fitted to the tool, but as you may be able to see, The finger guard is preventing the chuck from being screwed down the thread far enough.
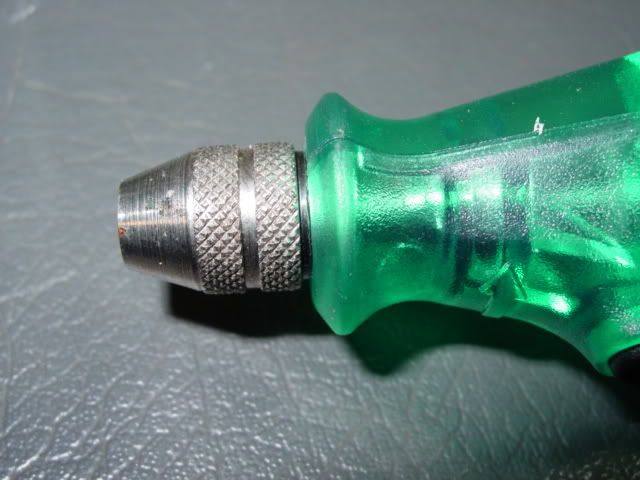
Time for our first bit of surgery. The finger guard, as the name suggests, protects your fingers, but doesn't have any other effect on the operation of the tool. Most rotary tools have removable finger guards, but this little budget fella doesn't, so out comes Mr Hacksaw. I removed the case , then sawed the guard section of both halves before re-assembling.
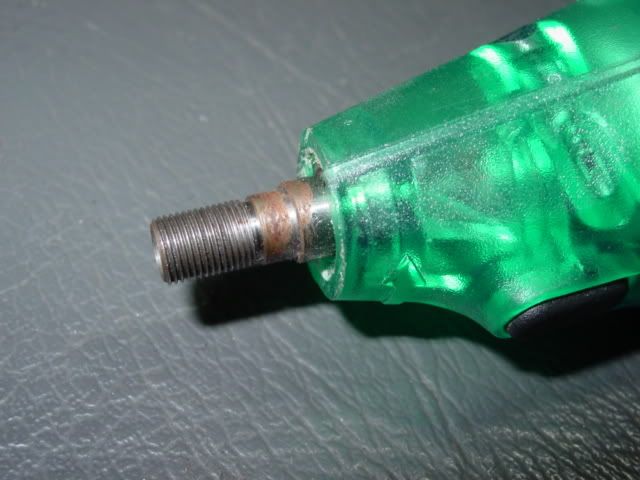
(Now at this point I must stress that I'm not suggesting you take a saw to your expensive power tools, and removing guards is obviously inherently dangerous and good for warranty-voiding. This tute is just for novely information purposes

Tadaa! The chuck now screws all the way down the thread! First success!
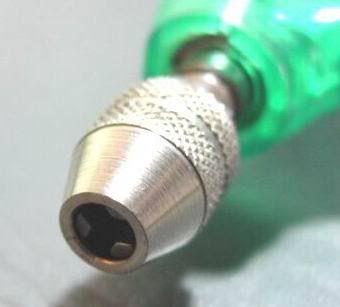
Ah, right. As the more observant of you may have noticed, even though the chuck is wound all the way down the thread, the jaws have not closed. Bit of a problem, as winding the chuck down the thread is supposedly how you close the jaws.
Look at the first pic again. That little circley thing in the centre of the chuck is the base of the jaw mechanism. As you turn the chuck down the thread, this should come into contact with the inside of the threaded bolt, and close the jaws. Must be that something is missing from our tool, and hence the chuck is not closing as it should.
What we need to do is find something that will fit down the centre of the bolt, and come into contact with jaws as the chuck is tightened. I've gone for a bit of brass rod, it was the exact diameter I needed, and with a bit of trial and error I was able to get the length right. I also rounded off the edges on the buffer to prevent any burrs from fouling the mechanism. You could probably use plastic rod, any sort of metal rod or tube, a section cut from a bolt. If you have a spare collet, like the one shown in the pic, you could use that; just hacksaw off the jaws.
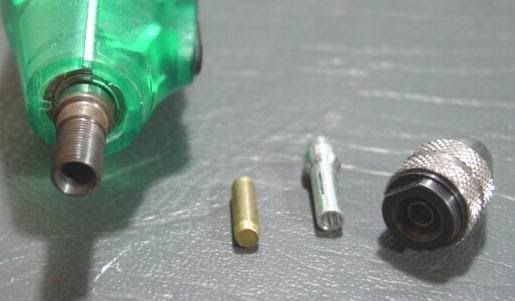
Slide the rod into the threaded bolt...
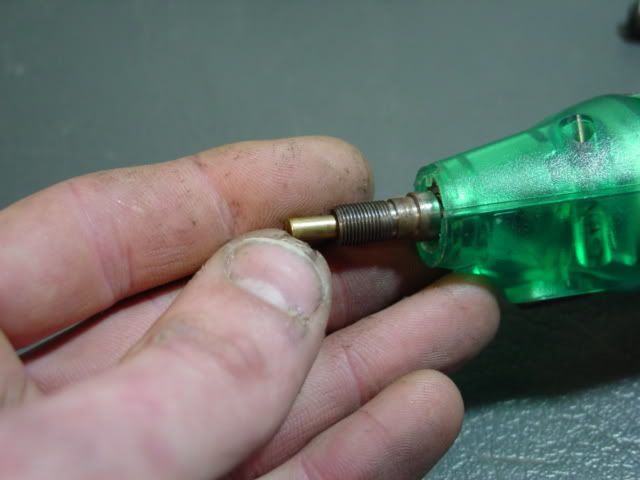
... wind on your chuck...
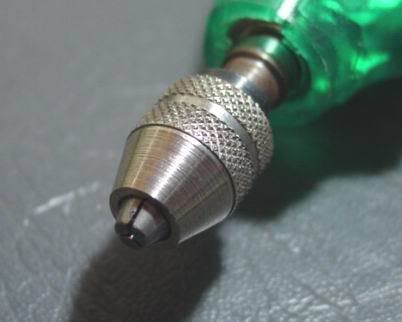
...et voila